

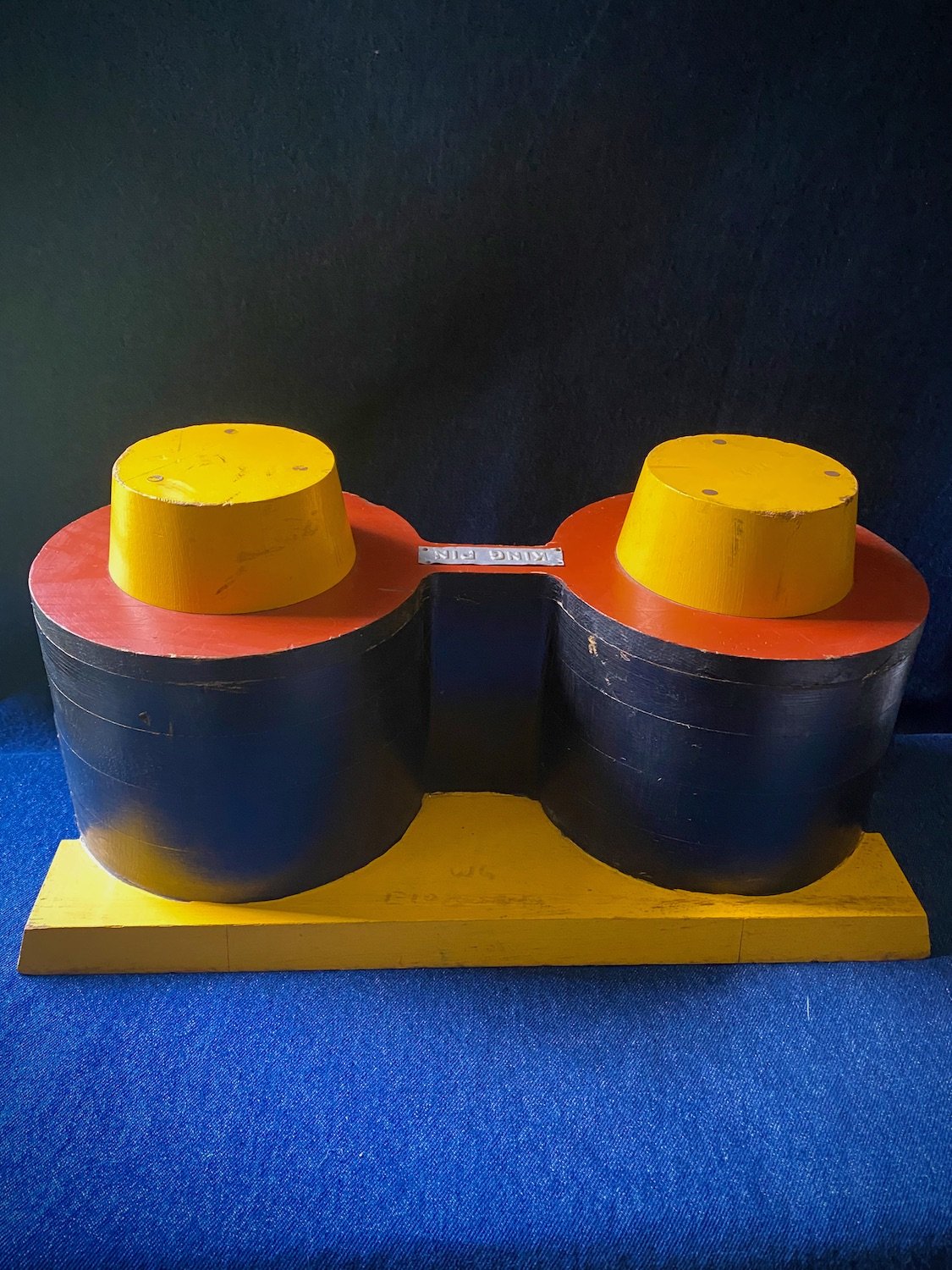
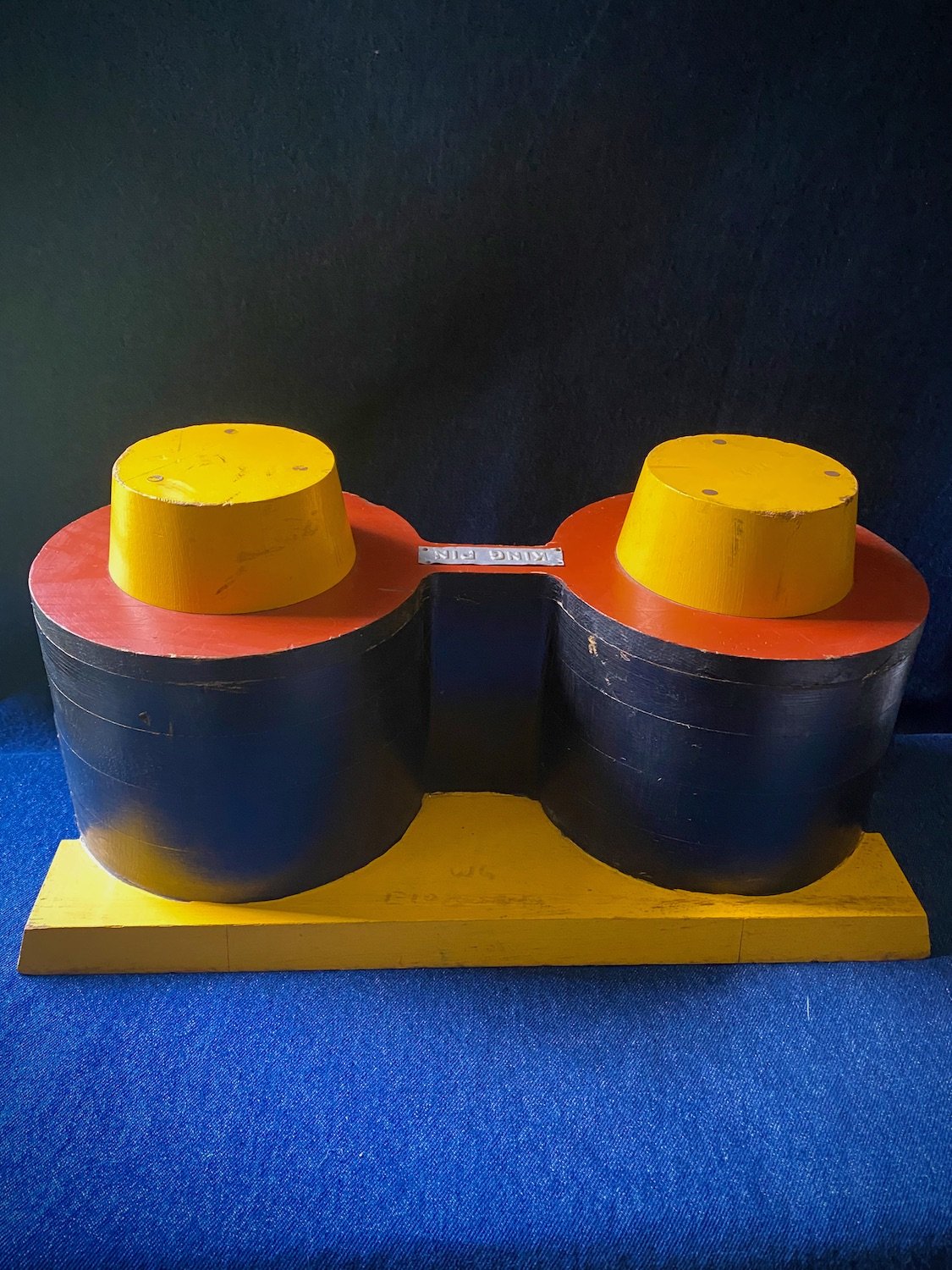
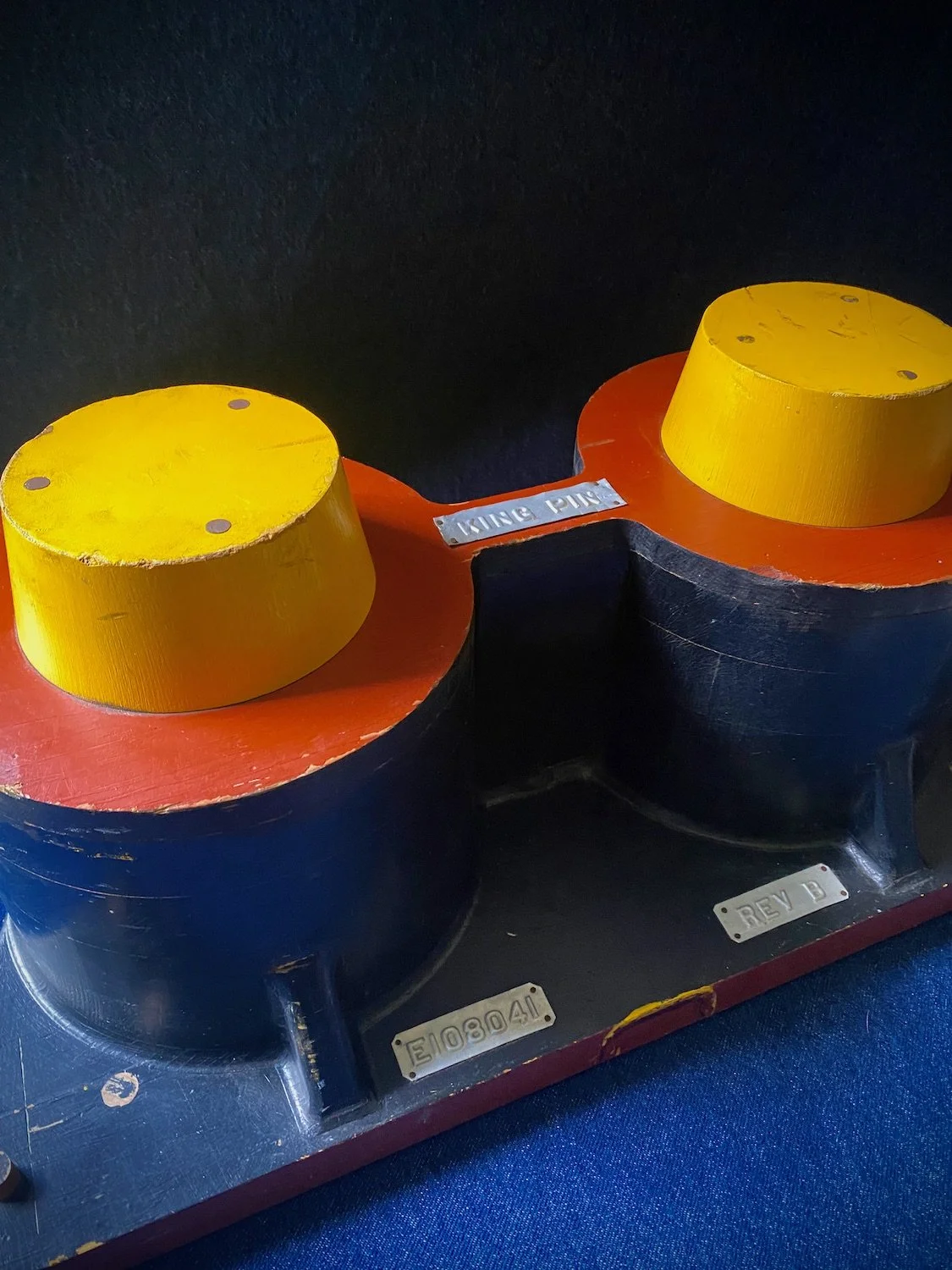
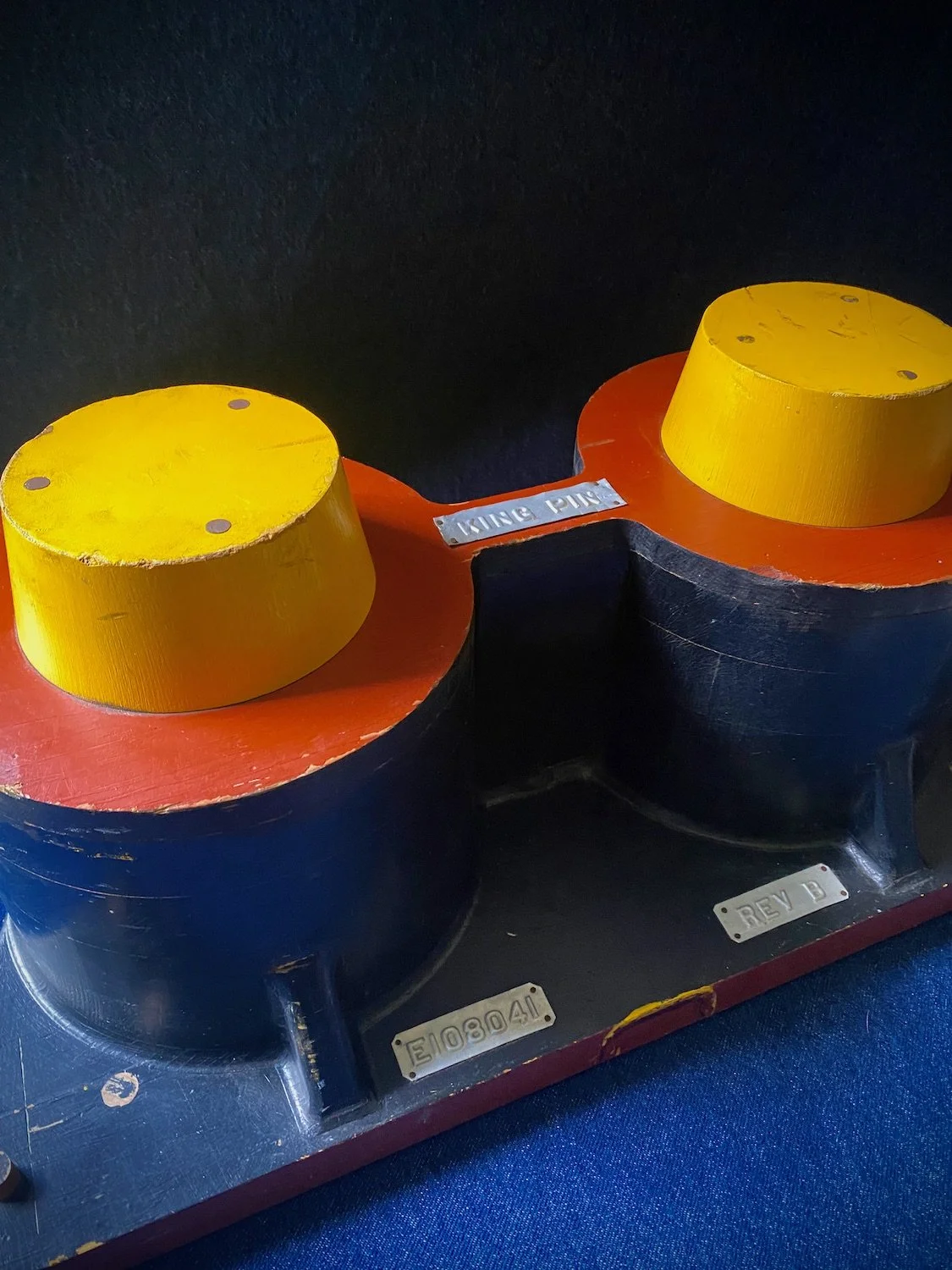

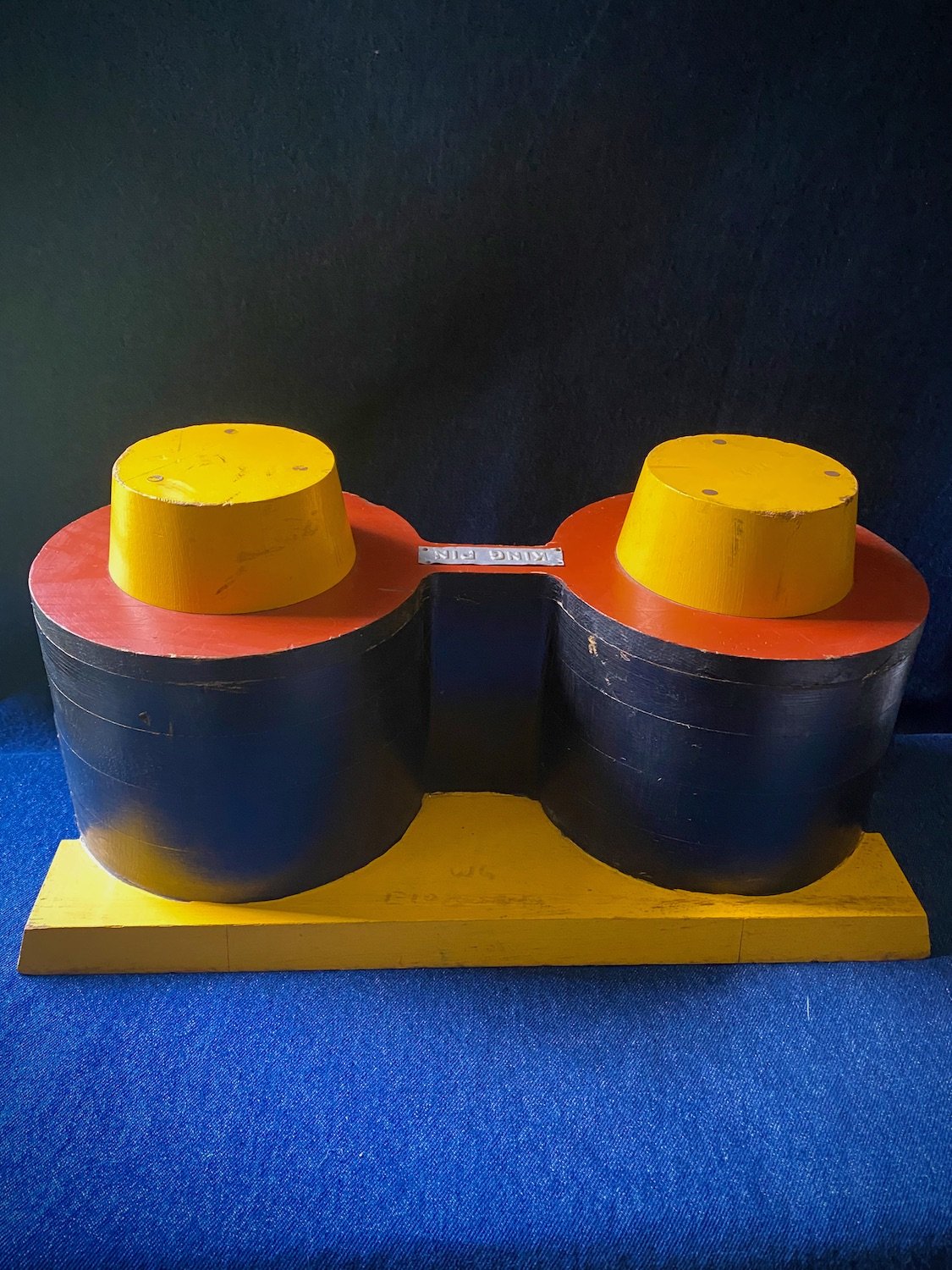
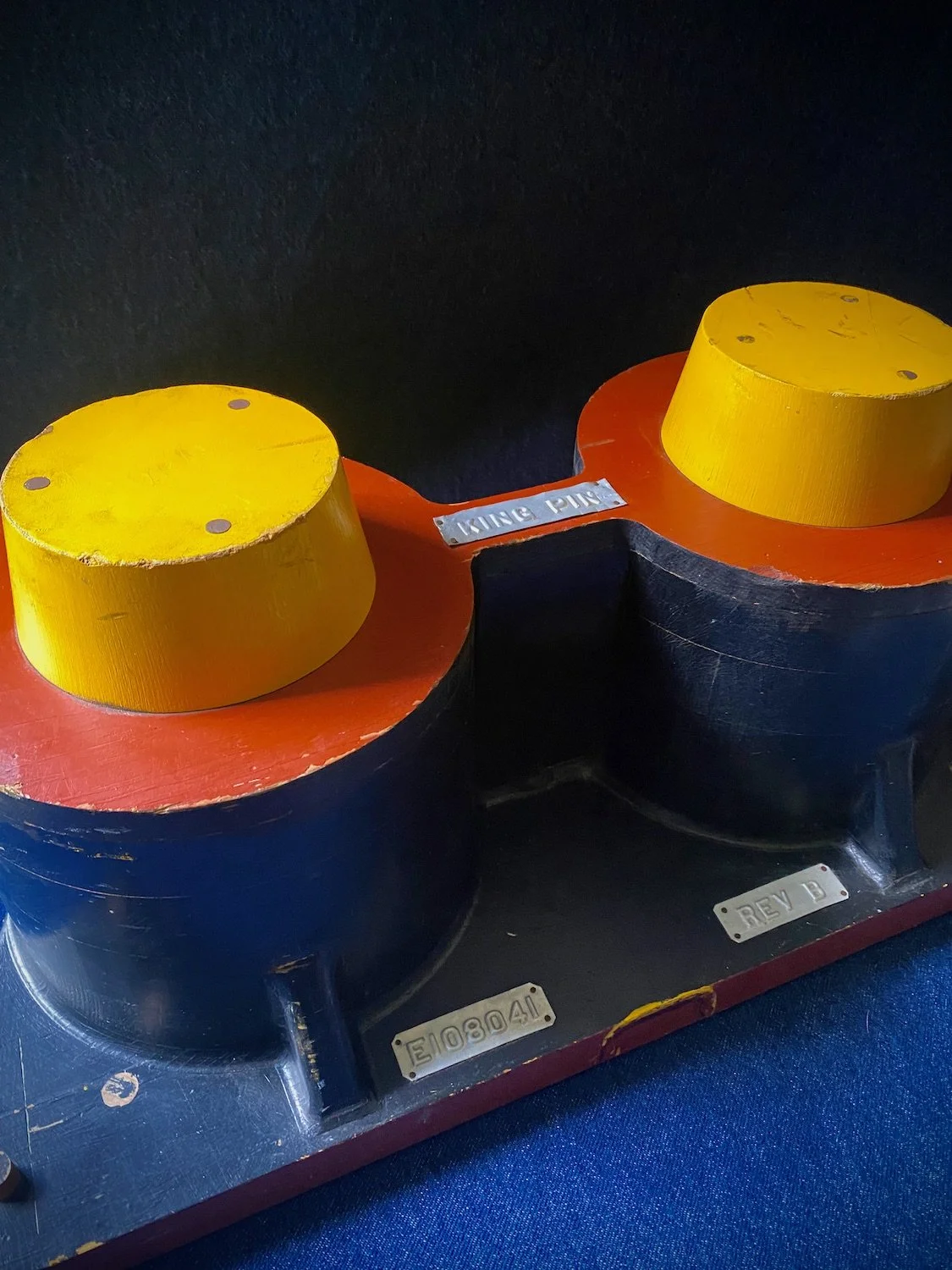
"King Pin" Foundry Pattern
Ever wonder how the iron bones of our industrial infrastructure were made— the giant turbines, gears, valves, et cetera? Here’s how. An engineer would submit a drawing for whatever they needed to a casting foundry. A skilled carpenter called a pattern-maker then turned the drawings into three-dimensional forms (patterns), made of wood. These forms often have multiple parts, which fit together like a puzzle. The forms would be nestled into a special type of sandy clay, creating a negative mold. Molten metal was poured into this, and voilà! — the original idea was made real. The patterns were dusted off, repaired, repainted, and returned to the foundry shelves for later use.
If we use the past tense, it is because pattern-making is a dying art. There are very few foundries left in operation, in the United States, at least. That makes these bold industrial readymades all the more compelling, both as sculptural forms, and as historical artifacts.
21” x 11” x 9”
Ever wonder how the iron bones of our industrial infrastructure were made— the giant turbines, gears, valves, et cetera? Here’s how. An engineer would submit a drawing for whatever they needed to a casting foundry. A skilled carpenter called a pattern-maker then turned the drawings into three-dimensional forms (patterns), made of wood. These forms often have multiple parts, which fit together like a puzzle. The forms would be nestled into a special type of sandy clay, creating a negative mold. Molten metal was poured into this, and voilà! — the original idea was made real. The patterns were dusted off, repaired, repainted, and returned to the foundry shelves for later use.
If we use the past tense, it is because pattern-making is a dying art. There are very few foundries left in operation, in the United States, at least. That makes these bold industrial readymades all the more compelling, both as sculptural forms, and as historical artifacts.
21” x 11” x 9”
Ever wonder how the iron bones of our industrial infrastructure were made— the giant turbines, gears, valves, et cetera? Here’s how. An engineer would submit a drawing for whatever they needed to a casting foundry. A skilled carpenter called a pattern-maker then turned the drawings into three-dimensional forms (patterns), made of wood. These forms often have multiple parts, which fit together like a puzzle. The forms would be nestled into a special type of sandy clay, creating a negative mold. Molten metal was poured into this, and voilà! — the original idea was made real. The patterns were dusted off, repaired, repainted, and returned to the foundry shelves for later use.
If we use the past tense, it is because pattern-making is a dying art. There are very few foundries left in operation, in the United States, at least. That makes these bold industrial readymades all the more compelling, both as sculptural forms, and as historical artifacts.
21” x 11” x 9”